前纺知识——高速纺丝工艺路线
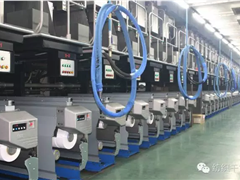
常规纺丝的纺丝速度低,故生产能力低,且制得的初生丝取向度低,结构不稳定,其性质随着放置时间的长短而差异很大,不能直接用于变形加工。随着纺织加工技术的进步,在20世纪70年代初在常规纺丝机的基础上发展了高速纺丝机。同常规纺丝相比,高速纺丝得到的初生丝具有一定的取向度,性质稳定,可以直接进行拉伸变形以制取变形丝,从而省去拉伸加捻工序,缩短了工艺流程。国外的涤纶高速纺丝技术得到迅速发展,至今已有90%以上的长丝采用高速纺丝技术。我国从20世纪80年代开始引进高速纺丝技术和主要设备,并逐步走上了开发新产品、国内自己制造生产设备的道路。
高速纺丝的初生丝称为预取向丝或部分取向丝(POY)。它比常规纺丝的未拉伸丝(UDY)的取向度高;与一般拉伸丝相比,取向度低,结晶度极低。
POY可直接进行拉伸变形加工而制得DTY变形丝。通常将整个高速纺丝拉伸变形工艺过程称为涤纶POY-DTY技术,简称高速纺丝工艺路线,其产品即拉伸变形丝(DTY)称为涤纶低弹丝。与常规纺丝相比-高速纺丝在技术经济方面有以下特点。纺丝卷绕速度高,POY的存放稳定性好.卷绕筒子硬度高、重量大、便于运输,设备简化,操作容易,纺丝过程稳定,适宜DTY加工,建设投资、能耗和产品成本较低。
一、POY性能的要求 POY是半制品,因此POY的性能好坏直接影响其后加工性和成品质量。为了确保后加工的顺利进行和成品的质量,要求其卷绕成形、退绕性能和后加工性能好,在放置和运输过程中品质变化小。具体有以下要求。
1.双折射率
双折射率在0.025以上,但不超过0.060。这是因为双折射率过低的POY,大分子取向度低,纤维结构不稳定,不适合直接进行变形加工。若双折射率过高,纤维大分子取向度和结晶度高,使纤维的后拉伸性能变差,在拉伸过程中会产生毛丝、断头。
2.结晶度 结晶度应小于30%,愈低愈好。若结晶度大,会造成后拉伸困难,并且拉伸后丝线的结构完整性差。因为初级结构愈完善,拉伸对原有结构的破坏就愈大,新结构的形成也愈不完整。
3.断裂伸长率及其不匀率 断裂伸长率在70%~180%之间,最好为100%~150%。若断裂伸K率太小,纤维的自然拉伸倍数也低,拉伸性能差,成品DTY毛丝多;若断裂伸长率太大,会增加后拉伸倍数,致使POY变形加工的适应性变差。尤为重要的是伸长不匀率(指丝筒与丝筒之间,同一丝筒的丝层之间),若伸长不匀率大产品质量波动就大。
4.结构一体性参数和沸水收缩率 结构一体性参数和沸水收缩率是反映纤维结晶和取向的指标,其测量比结晶度和取向度 方便易行,故生产上广泛使用这两个指标,要求结构一体性参数在0.8~1.0范围内,最好为0.4~0.9。若结构一体性参数大于1.0,说明纤维的取向度、结晶度低,断裂伸长度高(超过180%),纤维的预取向太低,不能作为POY使用。当结构体性参数小于0.3时,纤维取向度很高,并有两次结构(准结晶)形成,这种POY的断裂伸度低(小于70%),纤维的后拉伸性能差,加工时易产生毛丝和断头。
沸水收缩率要求为40%~70%。
5.丝条的摩擦系数 丝条的摩擦系数要求小于0.37,最好在0.2~034之间。摩擦系数低,丝条与导丝器或罗拉之间的摩擦力小,纺丝张力可降低,可减少毛丝和断头。但摩擦系数太低时,过小的摩擦力会导致丝条和摩擦盘问发生打滑,影响产品的质量。
6.含油率和油剂类型
含油率要求为0.3%~0.4%。若油剂含量太高,会造成POY在加工为DTY的过程中白粉增多;若含油不匀率过高,会使成品丝产生僵丝、染色不匀等。油剂的类型应适应后加工的要求,不污染加工器件,具有抗静电性,并与弹力丝油剂、织造油剂有亲和性,不使机械部件生锈,不影响丝条的染色均匀性等。
7.线密度及其不匀率
POY的线密度为成品丝的线密度与后拉伸倍数之积。对于要求同一DTY成品线密度的POY可能有不同的线密度。这是由于POY生产时采用不同的纺丝卷绕速度造成的。
线密度不匀率是一个较为重要的质量指标。若POY的线密度不匀率过大,说明POY生产不稳定,其内在质量差,不仅影响DTY产品的线密度不匀,而且可能影响DTY的内在质量。
8.强度及强度不匀 POY的强度不能过低。若强度过低,会使后加工过程中拉伸张力太低,从而造成DTY加工不稳定,而且强度过低的POY在后加工过程中容易受损伤而使最终产品质量差。若强度太高,后加工时拉伸张力高,也极易造成拉伸不匀和单丝断裂从而产生毛丝。强度不匀是衡量POY内在质量优劣的指标之一,其值应小。若强度不匀率高,会造成最终成品的不匀率高。
9.条干不匀率 乌斯特的平均差系数(U%)应小于1.2%,变异系数(CV%)应小于1.45%。若条干不匀率太高,会造成DTY加工不稳定,使成品丝的不匀率增加,僵丝和毛丝增多,尤其使匀染率 (M率)降低。
10.丝条单丝之间的集束性 丝条单丝之间的集束性要求丝条引出10~150cm后单丝仍不松散。集束性既不能太好,也不能太差。因为集束性太好,加捻时易引起丝条的纠结;集束性太差,丝条在行走时会发生各单丝间的滑移,影响拉伸的均匀性,容易产生松圉丝。
11.POY卷装成形良好 POY的卷绕筒子要求硬度适中(肖氏硬度为60~70)、不塌边、不叠边、无蛛网丝、尾丝丝圈清楚、不过多或过少等,退绕性能良好,能一根退到底.顺利接上尾丝,不产生刮毛现象。
二、纺程上熔体的变化 熔体纺丝纺程如图10-1所示。熔体以一定的泵供量从喷丝孔中挤出,喷丝孔直径为d0,平均速度为υ0,挤出温度T0。卷绕装置离喷丝板距离为L时,卷绕速度为uL,丝条的直径为dL,丝条的温度为TL。在纺程上,熔体喷出时发生剪切形变、喷出嘭化、拉伸形变、细流的冷却和固化以及初生丝的超分子结构形成。
熔体沿纺程发生直径和速度的变化:纺程一般可分成如图10-1所示的四个区域。第一区为熔体在毛细孔中的剪切流动转向出喷丝孔的膨化区。第二区为熔体在纺程上的拉伸流动。在该区中,熔体细流被迅速拉伸而变细,它的直径迅速减小,速度迅速上升,速度梯度也迅速增大。第三区为熔体细流的单轴拉伸形变。熔体细流沿纺程的速度继续增大,但其增加速率逐渐降低。由于熔体温度降低,熔体粘度增加,致使大分子取向度增加,双折射上升。该区是熔体细流向初生纤维转化的重要过渡阶段,该区域的终点即为凝固点。第四区为塑性形变区,熔体细流已凝固,丝条直径和速度不再发生变化。
三、纺程上丝条取向结构的形成
1.纺程上丝条取向的发展 熔体在喷丝孔中流动时,由于温度较高、松弛时间短,形成的取向很小。再者,即使有流动取向,在挤出膨化区时也将松弛殆尽。所以大分子的取向发展主要发生在第二区到第四区。第二区约在纺程上5~85cm,当小于48cm左右时,虽然熔体在形变的同时大分子产生取向,但由于温度高,解取向与取向同时发生,因而熔体的双折射率几乎为零;在48cm以后,双折射率迅速上升,此时熔体温度降至200℃左右,细流的速度梯度为du/dχ≈201/s。第三区在纺程上85~120cm,当χ在100cm附近时,熔体的速度梯度达到最大值,取向结构发展很快,双折射迅速增加。第四区在纺程上120cm以后,熔体的速度梯度趋向于零,流变阻力也降至零,随着纺程的延长,由于空气的摩擦阻力作用,卷绕张力增加,但对纺丝成形已无影响。
纺程上各区位的划分,随着纺丝速度的不同而不同(见表10—1)。由表10—1可知,随着纺速的增加,纺程上双折射发展加快,凝固点距喷丝板的距离缩短。
2.双折射与张应力的关系 在常规纺速范围内,纺程上丝条所受的张应力σ与双折射△n的关系符合Hamana公式:Δn=7.8×10-10σ。但实践证明,随着纺丝速度的提高,张应力与双折射之间的关系愈来愈偏离这一公式。当纺速达到4000n/mln时,该公式就不适用。这是由于随着纺丝速度的提高,张应力增大,使取向增加,取向又促进了结晶;当纺速达到4000m/min以上时,纺程上明显产生结晶。有研究表明,纺速在2500~3500m/min范围内,纺丝速度与双折射△n、张应力σ有如下经验公式:
3.双折射与结晶的关系
在高速纺丝时,纺程上的取向促进了结晶。根据Harnana公式,可将PET无定形区的双折射写成△n=CKσ。式中:C为常数;K为应力集中系数,可取1。而根据Stein公式,平均双折射应等于晶区和无定形区的双折射之和,则有式(10-1)的关系:
式中:θ为X-射线衍射法测定的结晶度;△ncr为晶区双折射(等于0.22);△nam为无定形区双折射(等于0.237);fcr为结晶取向因子;fam为无定形区取向因子。
式(10-1)简化后,fcr近似等于1,将Hamana公式代入得:
有研究表明,在纺速3000m/min时,由测得的纺程上的△n和σ计算出的结晶度为4%,与用密度法测得的结晶度接近。
高速纺丝时,POY不仅发生取向,同时产生结晶。POY的结晶主要受纺丝卷绕应力和分子取向的影响。
四、喷丝孔吐出量对纤维成形的影响 纺丝时,因纺制产品的线密度不同,使喷丝孔的吐出量不同。当纺丝速度相同时,若喷丝孔的吐出量下降,则丝条在纺程上所受的应力增加。这有利于POY的取向和结晶。
1.喷丝孔不同吐出量时的纺丝现象 当纺丝速度不变,而喷丝孔吐出量逐渐降低时,有下述现象发生:
①当喷丝孔吐出量逐渐降低时,纺程上纤维的凝固点距喷丝板的距离愈来愈近,如图10—2所示。由图可见,当喷出量下降到某一值时,纺程上纤维直径急剧下降,到此直径后就不再变化,这一现象称为细颈现象,即纺程上出现了细颈拉伸。这与固定吐出量、纺丝速度提高到一定值时纺程上出现的细颈现象相同。当吐出量下降,纺程上凝固点处所受的张应力σ上升,当张应力增加到足以克服纤维屈服点应力时,便发生细颈现象。
②随着喷丝孔吐出量的变化,初生丝的收缩率如图10—3所示。由图可见,随着喷丝孔吐出量的降低,收缩率先上升到一极大值,然后逐渐降低。这与吐出量固定时随着纺丝速度增加初生丝收缩率的变化情况相同。
2.喷丝孔不同吐出量时的纤维结构变化
(1)取向结构。喷丝孔吐出量与初生丝的双折射△n、声速取向因子fs的关系如图10-4所示。由图可见,在吐出量较大的区域,随着吐出量的降低,双折射△n上升缓慢,而声速取向因子fs急速上升;在吐出量较小的区域,随着吐出量的降低,双折射△”急速上升,而声速取向因子fs上升缓慢。双折射△n是晶区取向与非晶区取向的总效果,反映的是小尺寸的链段取向。声速取向因子fs是晶区与非晶区的平均取向,反映的是整条大分子链的取向情况。因此,图10-4说明在吐出量较大的区域,随着吐出量的降低,初生丝的大分子链的取向迅速增加;而在吐出量较小的区域,随着吐出量的降低,初生丝的大分子链段的取向迅速增加。这与纺丝速度增加时初生丝取向结构发生的变化相似。
(2)结晶结构。纺丝速度相同、喷丝孔吐出量不同所制得的初生丝试样的差示扫描量热分析的Dsc曲线与固定吐出量、不同纺丝速度时的DSC曲线相似。当吐出量不变时,随着纺丝速度的增加(或纺丝速度相同时,随着吐出量的降低),结晶温度Tc向低温移动,结晶熔化温度Tm向高温移动。这是由于初生丝的结构逐渐完善,所以在进行热分析测定时,使试样进一步结晶的Tc峰可能在较低温度下出现。原始结构较完整的试样,使其进一步熔化,需要在较高温度下才能出现Tm峰。
(3)力学性质。当纺丝速度相同,随着喷丝孔吐出量的降低,初生丝的应力一应变曲线的细颈拉伸部分逐渐缩短,即自然拉伸比逐渐降低,强度升高。当吐出量下降到0.482g/min时,初生丝的应力一应变曲线上的细颈拉伸消失。但初始模量随着吐出量的降低变化较小。由此可见,纺丝过程中纤维结构的形成不仅与纺速有关,而且与喷丝孔吐出量有关。纺程上纤维结构的形成是纺丝应力与冷却效果的综合反映,而纺丝应力起主导作用。纺丝线上出现细颈形变是纺程上的丝条结构发展到一定程度的结果,可能导致纺程上的纤维结晶。